Leverantörer
Supplier instructions
Kockums Maskin AB (KMAB) delivers products to the automotive and the engineering industry with demands for short terms of delivery and just-in-time shipments and special demands for quality and environment management.
KMAB requires from their suppliers that they will comply with the following items:
Suppliers to KMAB must contribute towards achieving and implementing the objectives of the KMAB quality- and environmental policies and must promote continual improvement.
Our suppliers are by signing this document ensuring the confidentiality of our/our customers products and projects, including documentation and conversations. This demand shall also be secured by all sub-suppliers.
KMAB suppliers shall comply with the requirements in IATF 16949 or at least, those of ISO 9001 with an initiated process to reach the ultimate goal of certification to IATF 16949. Suppliers shall also comply with requirements in ISO 14001. Any changes in the status of certification shall be provided to KMAB directly.
In general, KMAB, expects that all suppliers comply with all applicable national and international legal requirement. Suppliers has sole responsible to ensure that all sub-suppliers comply with applicable regulations/guidelines and legal requirements.
Suppliers shall comply with all applicable REACH and IMDS (mtrl data system) requirements that affect the products that they supply to KMAB.
KMAB are committed to CSR aspects and transfers this commitment to all suppliers and expect all suppliers and sub-suppliers of products/processes/services to adhere to CSR guidelines and conflict minerals legislation.
Suppliers must not supply product and substances that are present on our customers lists. Suppliers must ensure that the latest version of the list is used and is solely responsible for ensuring updates are communicated. Latest versions can be found at Volvo’s and Scania’s homepages.
KMAB uses several audit/assessment tools to ensure suppliers meet appropriate quality levels. Audits may be conducted by external auditors, KMAB employees or KMAB customer representative.
KMAB will make frequent Supplier Evaluations. The target of the supplier evaluations is to identify and report good and bad supplier performances and make opportunities for improvements visible and transparent.
The evaluation will be based on objective metrics measured by KMAB and contain on-time/full deliveries, rejected parts, rework/sorting at KMAB, complaints, audit results and if the requirements is not fulfilled an escalation process may be started at KMAB.
At manufacturing of initial samples the demands in AIAG:s “Production Part Approval Process, valid edition” shall be followed. The level of PPAP is written in the sample order from KMAB.
Deliveries of initial samples shall be marked with “INITIAL SAMPLES” and item number. PPAP documentation shall be sent according to the order. Deviation from this procedure must be approved by KMAB.
Deliveries shall be performed in correct time and with ordered quantity. The consignments shall be marked with signed evidence that the products comply with requirements.
The products shall be protected against rust and other potential defects. The deliveries shall be notified one day before shipping or latest at the shipping time.
At any kind of deviation or hesitation, contact KMAB logistics- or quality department for consultation.
Sorting costs and other costs, which are results of incorrect deliveries, will, after agreement, be transferred to the supplier.
When KMAB can correct the deviations, 500 SEK/Hour will be charged. If the use of an external source will be necessary, the real cost will be charged (min. 1000 SEK).
Not approved excess deliveries will be sent back and charged with transport costs.
Logistics Department: +46 457 78505
Quality Department: +46 457 78526
Contact
Should you have any questions about our supplier instructions, feel free to contact us.
Logistics department: +46 457 78505
Quality department: +46 457 78526
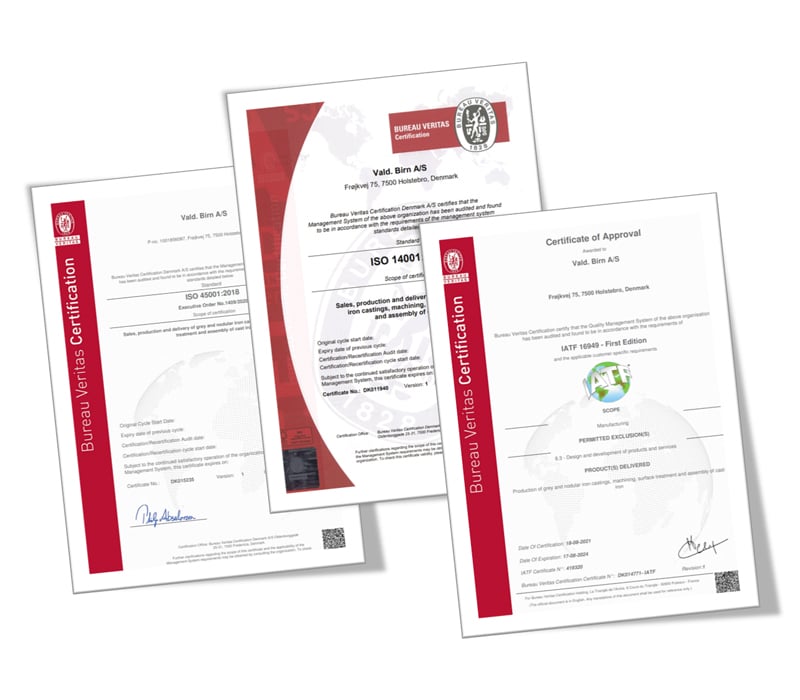